3 Things That Make a Quality Home Inspector
Often I am asked what exactly is a quality home inspector looking for during a home inspection. I usually go down the list in bullet point fashion, but the top three things that are most important to any home buyer are almost always the first three things I list off.
I wanted to cover these thee topics in greater detail below.
1. Roof Inspection
First, I always start with the roof. Knowing how to read a roof is critical to being a quality home inspector, and it is easy to say the roof is the most important thing I look at on a daily basis. The roof is the protection between you and the elements. Even when you watch movies that are set in exotic places (Blue Lagoon, Tarzan, Castaway and The Beach, etc.) the one thing they all have in common is crudely constructed enclosures with a roof over head. None of those encampments had walls, just a way to keep a roof over one’s head does a lot to keep a person healthy. It shields the sun and keeps you dry when it rains. A roof is by far the most important necessity to any living quarters.
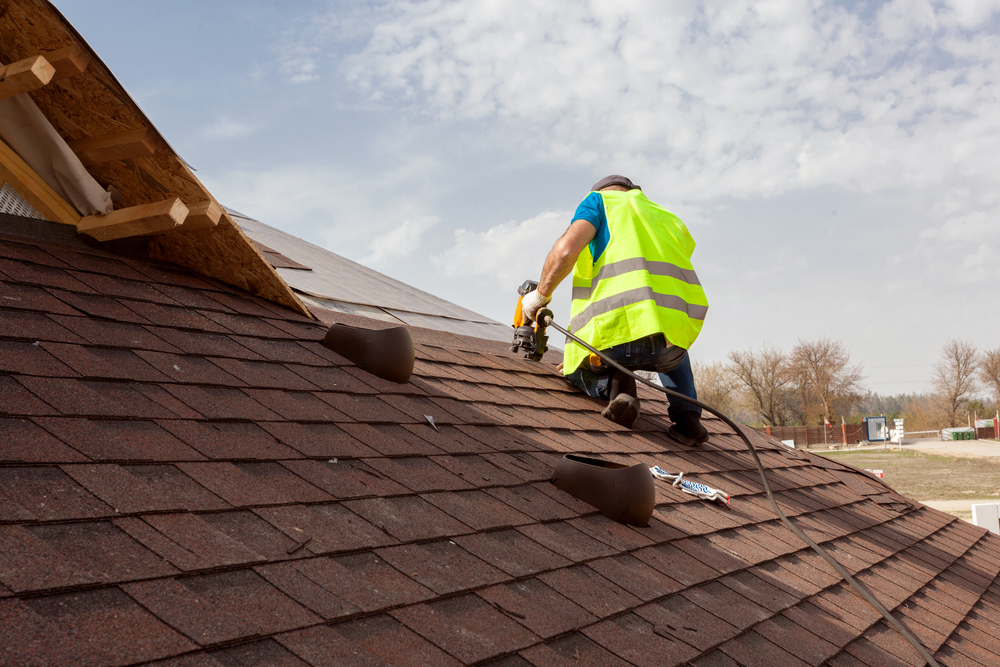
A quality home inspector will inform you exactly what kind of condition your roof is in.
While inspecting the roof I look for many different things. The type of covering, the quality of that covering, and how well it was installed. There are different type of roof coverings with some variations. For example, the most common roof covering installed are composite shingles. There are three-tab roofs which have a life expectancy of 20 years from installation, and there is a composite product referred to architectural shingles which carries a 30 year life expectancy. There are different types of architectural composite shingles that supposedly have a longer expectancy than 30 years, but they haven’t been offered long enough to truly test if they are worth the extra expense. Longer than 30 years is a long time to be exposed to the sun’s brutal intensity, not to mention the rains and winds.
Beyond the composition products, there are metal roofs that have a longer life expectancy. Even though these roofs are superior in material, they can still go bad. First, you really have to research the installer. Any roofing company can get into installing metal roofs, but does the crew really know what they are doing? John Deere is a great tractor, but who’s driving it? If I decide to walk a metal roof during my roof inspection, I’m looking for sealants added. If I start seeing caulking applied at the joints, I know the roof’s integrity is blown. Now, there is a big pile of junk overhead that could leak at any time. But since it was already so expensive to install, the owner of the roof is really married to it. If you buy or already own a metal roof and you need to make a modification to it, such as a vent or a skylight, make sure you use the installation company who put the roof on. This way, if there is a warranty left on the roof, you won’t automatically void it by making such changes to the product. Don’t get me wrong, the installer may not stand by the product, but at least you went about it the correct by by contacting them first.
I also come across wood shingles during roof inspections, as well as tile (cement or terracotta). I won’t walk on either one of those. Wood shingles have a life expectancy of 25 years, and if you notice the shingles turn white that means it is time to have them replaced. Most people opt to have them replaced with composition shingles, but you cannot apply composition shingles over wood shake roofing. The composition never lays flat and ultimately the material starts to look wavy and doesn’t usher the water down the surface as quickly as it would if there was a flat surface to glide down. It is against the International Residential Code (IRC) to place composite roofing over wood shingles for these reasons. I can look at a roof and say with certainty that there is a wood shake roof at the base of the roofing layers.
During the roof inspection, I also look at the plumbing penetrations and their weatherized rubber membranes. These are referred to as “no caulk” boots. They fit snugly around plumbing vent pipes and provide a water tight seal depending on how long they have been installed. The sun is a punishing force, and these rubber seals will crack eventually. In fact, they usually need to be replaced before the roof’s service life has ended. The roof covering and the flashings are the common details I look at, but often times there will be exhaust vents, skylights, chimneys and satellite dishes that penetrate the roof covering. I’m not going to go over those now, but they are examined for details that could lead to a leak in the roof.
2. Foundation Inspection
The second most important thing a quality home inspector looks at is the foundation. I will always see cracks because poured cement foundations shrink as they cure. Its not the cracks that get my attention, it’s the type of crack that I’m looking for that needs my judgement. The cracks I look for are called “V” cracks. The name says it all. If I see cracks in a foundation that are wider at one end than the other, I know with absolute certainty that there is a foundational issue. If a crack is wider at the top than the bottom, I know the foundation is sinking. And the thing about these cracks is that they must come in pairs.
The most obvious “V” crack I have ever seen was below the end unit of an attached three-story town home. What I believe happened was the ground was dug out too deep at this corner, and the builder allowed the surface to be back filled. It doesn’t matter how much compaction you do, or how heavy your equipment is, you can’t beat Father Time. As time goes by, soils compact more and more. Once the soil is removed, unless a structural engineer is on hand to plan how to install pillars that rest on the undisturbed soil below, it will take decades to get that stability back.
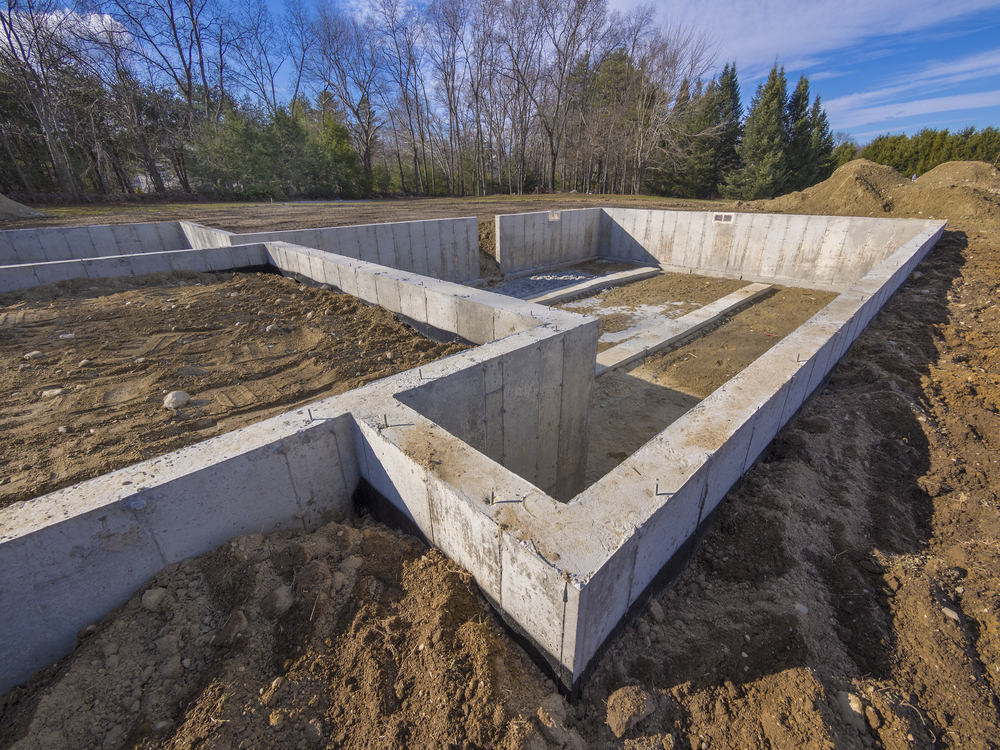
Foundation repairs are expensive. A quality home inspector can easily save you thousands of dollars if they understand foundations.
Now it is up to the builder to decide which is more expensive: the proper repair from an engineer and the time it sets the builder back, or the lawsuit they’re going to end up with once the foundation starts to settle. The most obvious way to know if a foundation is settling isn’t by looking at the foundation itself, but seeing the diagonal cracks above interior doors and windows with the same “V” pattern, wider at one side than the other. I show realtors these cracks when I get the opportunity so they can see them when they tour a house. Nothing better for the realtor than to be the hero and not allow their client to waste time and money on an inspection when there are alternate options available.
3. Exterior Siding Inspection
Lastly, on this most important list is the exterior siding. Any quality home inspector knows that like roofs, the siding is keeping out the elements to protect the wood framing and interior drywall or plaster surfaces. There is one siding out there that all inspectors need to know when they see it. Admittedly, sometimes I need to take a closer look as to not mistake it for something else, but when I see it I make sure the buyer knows as well. The siding is known at Louisiana Pacific AKA: LP or Hardy Board, or wafer board.
This is a wood composition product made of wood shavings compressed to create a siding. If this material gets wet and swells, it will make the fastening nail heads look as though they have puckered in. Once this happens, it will never return to normal. I have seen this LP siding in very good condition as well, and that tells me the owner of this property knows what he or she has and how to properly take care of it.
The key to this siding is painting it properly and not letting it go to long without a fresh seal. The main culprit that causes this siding to fail is the sun, as it will beat on the paint and crack it. Then the rains will come and the water will intrude into those gaps. Next thing you know, the siding has started to swell and more opportunities have developed for exterior siding failure. The key to the paint job is the drip edge. The very bottom of the piece of siding where water tension allows moisture to collect before it gains enough weight to drop to the ground.
When a person has a paint sprayer and is painting the side of a house, it is awesome. It is powerful. It is a big responsibility too. The airless sprayers cover the surface better than any application available, but the one thing that the person spraying doesn’t do is get down, (and I mean way down) onto the ground and spray upward at the last 6 to 8 inches from the ground where the drip edges are. Whether or not it is sheet style siding (4’ x 8’ sheets) or lapped boards with a 7 inch reveal, you have got to paint that drip edge. My advice is to use a roller. Sure you can spray it, but since it is incredibly difficult to actually see that you did it correctly, I advise physically contacting the materials with an applicator such as a small roller or paint brush. And be liberal about it. You’re already out there, you already spent all that time prepping to make sure the outcome is what you want it to be no matter if this a fee based job or you’re a homeowner doing it yourself. And don’t forget the corner trim boards too. They collect water at the base of the materials just as easily, and there are often made of wood, so dry rot can set in.
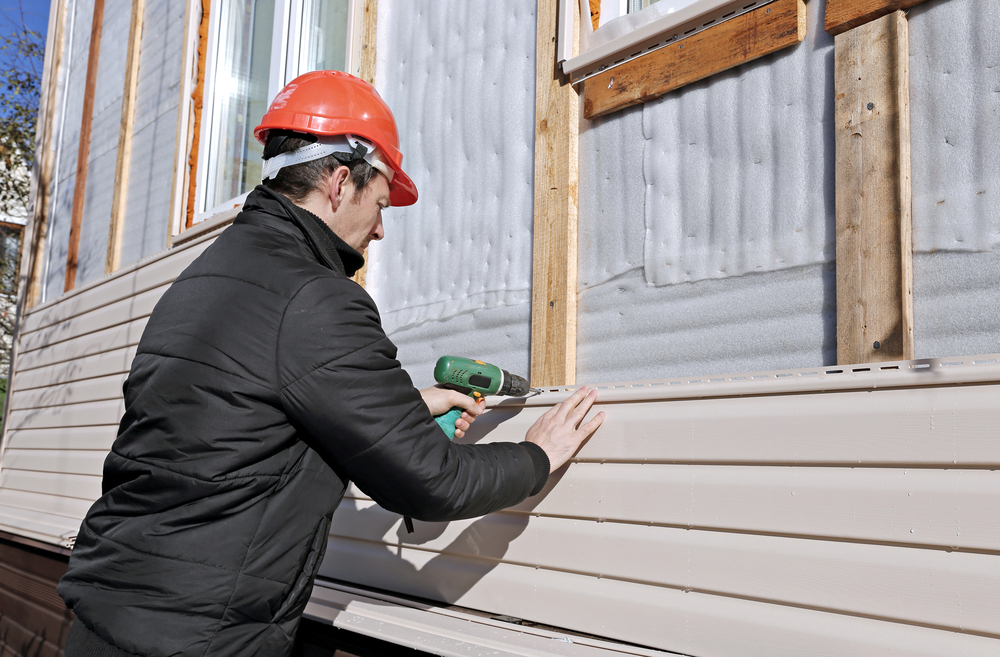
Last but not least, all quality home inspectors should know exterior siding like the back of their hand!
There are a lot of other siding options. I just went into detail about the LP siding because it has the worst Achilles heel of them all. The other sidings I will see are lapped wood plank, usually made of cedar to deter wood destroying insects, or cedar shake shingles, also made of cedar (and very expensive to have installed new due to the laborious nature of the small pieces of shingle), stucco, which is not common in the Pacific Northwest due to our marine climate, T-111, which comes in 4’x8’ plywood or OSB (Oriented Strand Board) sheets, and more.
My most favored siding is Fiber Cement AKA Hardi-Board. This material has made it to my favorite list because it can withstand the most punishment. Don’t get me wrong, I have seen Hardi-Boards in poor condition, but it was only when the crew left them out and they got rained on for two or more days without being installed. Hardi-Board is seen often on new construction and comes in a canary yellow primer color. Once they’re up and installed properly, I’ve seen them never get painted and last many years. When water is able to drip off of the material as it can withstand the elements better than any other product out there. The most common failure I see is when bulk rain water is accidentally directed toward it from a roof’s rain shed and there is no kick out flashing installed to direct the water into the gutter and it is allowed to flow between the gutter end cap and the siding. But under these circumstances all sidings will fail.
Although I covered a lot of information here, and I probably didn’t cover all of it and the different variations that can be experienced. If you’ve read this far, you got a good education from my life’s learnings in by quest to become the highest quality home inspector in Portland, OR.
Every day I go out to inspect homes, and every day I have a new experience. That’s what keeps me going! If you are interested in a quality home inspection from Octopus Home Inspections, contact me here.